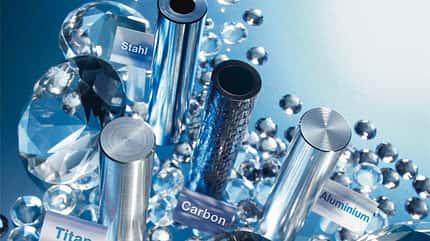
Unaufhaltsam schreitet der Kohlefaser-Boom voran. Rahmen und Parts präsentieren sich im edlen Carbonkleid und lassen die metallische Konkurrenz im Vergleich dazu oft alt aussehen.
Doch Metalle zählen noch lange nicht zum alten Eisen. Ganz im Gegenteil: Alu gilt nach wie vor als Material Nummer eins im Fahrradbau, und Stahl, Titan und Co. bringen Eigenschaften mit, die das schwarze Carbongeflecht vor Neid erblassen lässt.
Die Bauteile am Bike müssen enormen Anforderungen standhalten – und das über einen möglichst langen Zeitraum. Nur durch intelligente Konstruktionen und den Einsatz unterschiedlicher Werkstoffe gelingt der Drahtseilakt aus optimaler Funktion, geringem Gewicht und hoher Langlebigkeit. Das Hauptaugenmerk liegt dabei auf dem Rahmen – dem Kernstück des Mountainbikes. Aber welches Material ist das beste? Eine viel diskutierte Frage, die sich pauschal nicht beantworten lässt.
Zu unterschiedlich sind die jeweiligen Anforderungen und Bedingungen. Eines lässt sich jedoch mit großer Sicherheit sagen: Wer Rahmen mit höchster Steifigkeit und gleichzeitig unschlagbar niedrigem Gewicht sucht, kommt am Werkstoff Carbon nicht mehr vorbei.
Der Verbund aus Faser und Epoxidharz besitzt ganz klar das größte Leichtbaupotenzial. Zudem garantiert der geschickte Einsatz der hochfesten Faser annähernd verlustfreien Vortrieb und bietet gleichzeitig Komfort durch vertikale Elastizität. Ein Vorteil, der auf den anisotropen Eigenschaften des Faserwerkstoffes beruht.
Dabei verfügt der relativ neue Werkstoff Carbon noch über ungenutztes Potenzial – hat immer noch Reserven. „Während die metallischen Werkstoffe bereits ausgereizt sind, können wir mit Faserverbundwerkstoffen noch große Fortschritte bezüglich Gewicht und Haltbarkeit erzielen“, sagt Peter Denk, Chef von Denk Engineering und Carbon-Experte der ersten Stunde. Aber: Carbon bringt nicht nur Vorteile mit sich.
Schwierige Verarbeitung, hohe Material- und Fertigungskosten sowie schwer einschätzbares Bruchverhalten gehen ebenso auf das Konto des Werkstoffes.
Deutlich weniger problematisch zeigt sich in dieser Hinsicht der Werkstoff Alu.
Alu ist der Werkstoff Nummer eins
Aluminium gilt nicht nur als das am häufigsten vorkommende Metall in der Erdkruste, sondern auch als der am häufigsten verbaute Werkstoff bei Mountainbikes.
Zu Recht, denn das relativ weiche Material lässt sich hervorragend verarbeiten und bringt hohes Leichtbaupotenzial mit. Die Kosten fallen im Vergleich zu Carbon auch deutlich geringer aus. Alu gilt als erste Wahl für viele Hersteller und findet sich an fast allen Bauteilen am Bike wieder.
Es handelt sich dabei allerdings nie um reines Aluminium, sondern immer um eine Legierung – ein Grundmetall, dem zusätzliche Stoffe zugegeben werden, um bestimmte Eigenschaften zu erreichen.
Erst durch definierte Zusätze, wie etwa von Zink gelangt das Leichtmetall zu ausreichender Festigkeit, um den hohen Beanspruchungen auf den Trails zu trotzen.
Auch der Werkstoff Scandium wird in letzter Zeit wieder häufiger als Legierungsmaterial genannt. Das Material bewirkt bei Alu eine Verfeinerung des Gefüges und verringert so die Rissgefahr an der Schweißnaht. Dadurch lässt sich Material und somit auch Gewicht einsparen.
Die richtige Legierung allein reicht jedoch nicht aus, um einen hochwertigen Rahmen nach heutigem Stand der Technik zu fertigen. Erst durch Technologien wie Konifizierung oder Hydroforming gelingt der optimale Balanceakt zwischen hoher Festigkeit und niedrigem Gewicht.
Der große Durchbruch im Rahmenbau gelang mit Alu jedoch durch einen relativ simplen Konstruktionsschritt – Oversizing. Erst die typisch großvolumigen, dünnwandigen Rohre führten zu der bekannt hohen Steifigkeit. Stahl wurde als Rahmenmaterial fast vollständig vom Markt verdrängt. Aber nur fast, denn momentan erlebt der Werkstoff wieder eine Renaissance.
Die Wiedergeburt des Stahls
Stahl ist die Mutter aller Werkstoffe im Fahrradbau. Auch in den frühen Anfängen des Mountainbikesports gab es praktisch keine Alternative zu dem unverwüstlichen Material. Wer jedoch denkt, dass die Stahl-Ära in Zeiten von Alu und Carbon zu Ende geht, irrt. Nach wie vor bietet der Werkstoff Eigenschaften, mit denen andere Materialien nicht mithalten können.
Sehr hohe Zug-, Verschleiß- und Dauerfestigkeit und die bezahlbaren Fertigungskosten machen den Werkstoff für Teile wie Ketten, hochfeste Schrauben oder Tretlager-Achsen unersetzlich. Von einer ähnlich großen Sicherheit gegen Überlastbrüche sind Teile aus Carbon weit entfernt.
Aber auch im Rahmenbau steigt die Nachfrage nach dem altbewährten Chrom-Moly-Material wieder. Rahmenbauer verzeichnen mehr Anfragen als in den letzten Jahren. Nur ein Retro-Boom oder ein ehrliches Bekenntnis zu dem Werkstoff? Wahrscheinlich eine Mischung aus beidem, denn auch bei Stahlrohren hat sich in den letzten Jahren einiges getan. Verbesserte Legierungen bringen noch mehr Festigkeit, größere Rohrquerschnitte sorgen für höhere Steifigkeiten. Extrem flexende Rahmen gehören im hochklassigen Segment der Vergangenheit an.
Komfort bieten die Chrom-Moly-Rohre aber nach wie vor, schlucken Stöße und Vibrationen deutlich besser als etwa Alu. Ein Vorteil, der vor allem bei Hardtails zum Tragen kommt – wo kein Dämpfer die Schläge abfängt.
Als Nachteil von Stahl zählt neben hohem Gewicht die erhöhte Korrosionsgefahr. Spezielle Oberflächenbehandlungen müssen deshalb den schädlichen Rost verhindern. Ein Problem, das ein anderer Werkstoff nicht kennt – Titan.
Rahmen für die Ewigkeit
Titan bildet an der Oberfläche eine feste Oxidschicht, die vor weiterer Korrosion schützt und für den charakteristischen Farbton sorgt. Der Werkstoff besitzt eine Festigkeit, die fast so hoch ausfällt wie die von Stahl, wiegt dabei aber etwa 40 Prozent weniger. Optimale Eigenschaften, um Rahmen und Parts für die Ewigkeit zu bauen. „Titan ist das edelste und dauerhafteste Material – bei richtiger Verarbeitung ein wahres Schmuckstück“, schwärmt Titanexperte Bob Sticha.
Die relativ dünnen Rohre sorgen bei hartem Antritt nicht gerade für überragende Steifigkeit, liefern aber ähnlich wie Stahl sehr gute Komfortwerte und eignen sich deshalb ebenfalls optimal für den Einsatz an Hardtails.
Die sehr schwierige und aufwendige Verarbeitung und der exorbitante Preis verhindern jedoch den Einsatz in der Massenproduktion. Rahmen und Parts aus Titan gelten deshalb nach wie vor als exklusiv und bleiben entweder zahlungskräftigen Kunden oder besonders leidenschaftlichen Sammlern vorbehalten.
Mehr Bike Know-how:
Gewinnen Sie einen Volvo XC60:
Carbon: Edel und steif
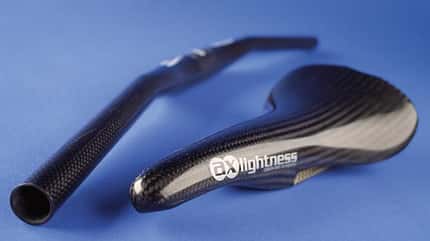
Der Verbund aus Kohlefaser und Epoxidharz fordert die metallische Konkurrenz heraus – trumpft dabei mit sensationellen Werten und Eigenschaften auf. Die Fasern besitzen etwa die vierfache Zugfestigkeit von Stahl und den bis zu sechsfachen E-Modul (Widerstand gegen Verformung) von Alu.
Um jedoch aus der Faser ein Bauteil zu fertigen, muss diese zuerst in eine Matrix (Epoxidharz) eingebettet werden. Dabei büßt der Werkstoff zwar einiges von seinen theoretischen Vorteilen ein, dennoch entstehen bei geschickter Fertigung Rahmen, die im Verhältnis Steifigkeit/Gewicht Bestwerte setzen.
Auch in Sachen Werkstoffermüdung kann die Faser punkten. Die ständigen Wechselbiegebeanspruchungen während der Fahrt steckt Carbon deutlich besser weg als die Konkurrenz aus Metall. Unterschiede gibt es allerdings auch zwischen den Carbonbauteilen.
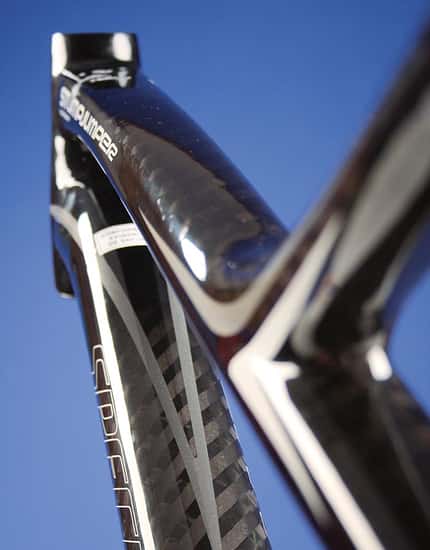
Es kommen sowohl HT-(High-Tensity-)Fasern als auch HM-(High-Modulus-)Fasern zum Einsatz. Letztere werden in einem zusätzlichen Arbeitsschritt geglättet, was einerseits die Steifigkeit, andererseits aber auch die Sprödigkeit erhöht.
Diese sehr teure Faser-Variante kommt vor allem in extremen Leichtbau-Produkten zum Einsatz. Die Anordnung der Fasern entscheidet ebenfalls über die Eigenschaften des Carbon-Teils. Uni-Direktional-Gelege (parallel angeordnete Fasern) kommen meist an hoch beanspruchten Stellen des Bauteils zum Einsatz – dort, wo die Kraftwirkung bekannt ist. Verwebte Fasermatten können Kräfte in mehreren Richtungen aufnehmen und bilden häufig die optisch ansprechende Deckschicht.
Auch Harze unterscheiden sich in ihren Eigenschaften. Neuere Produkte schützen etwa besser gegen Steinschlag. Carbon gilt in Fachkreisen als das Material mit dem größten Potenzial. Doch die Handhabung erweist sich als nicht ganz unproblematisch. Die Verarbeitung erfordert enormen Aufwand durch Handarbeit und eine ordentliche Portion an Erfahrung. Dem Faserverbundwerkstoff fehlt zudem das relativ gutmütige Bruchverhalten der Metalle. Bei falscher Verarbeitung können Rahmen oder Parts unvorhersehbar und schlagartig brechen.
Mehr Bike Know-how:
Gewinnen Sie einen Volvo XC60:
Aluminium: Perfekter Allround-Werkstoff
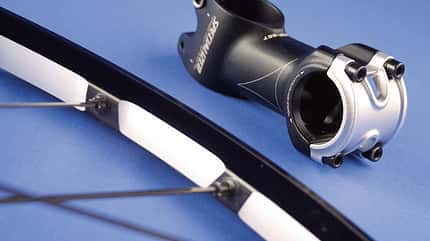
Aluminium gilt als der Allround-Werkstoff im Fahrradbau. Das weiche Material lässt sich einfach und kostengünstig verarbeiten und in fast jede beliebige Form bringen. Der große Durchbruch im Rahmenbau gelang aber erst durch die Verwendung von Rohren mit großem Durchmesser (oversize). Die Steifigkeit eines Rohres steigt nämlich in der dritten Potenz zum Durchmesser.
Durch die geringe Dichte des Materials (2,7 g/cm³) bleibt das Gewicht trotz der voluminösen Rohre aber sehr gering – superleichte Rohrsätze sind möglich. Innen- und Außenkonifizierung sowie Änderungen am Querschnitt ermöglichen zusätzlich Gewichtseinsparungen und eine Erhöhung der Steifigkeit. Gegen Korrosion bildet Aluminium, ähnlich wie Titan, eine fast undurchdringliche Oxidschicht an der Oberfläche.
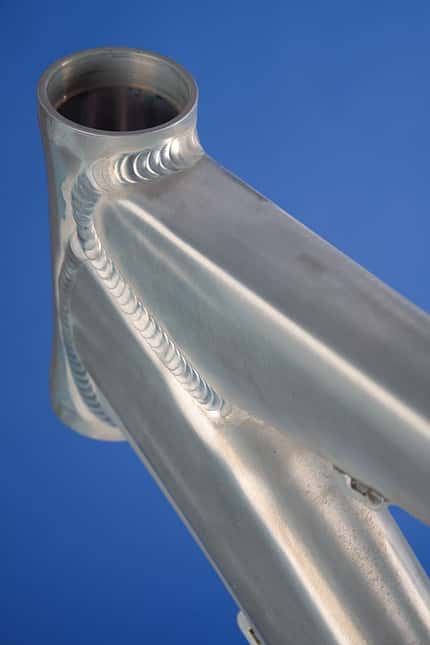
Aluminium tritt als Werkstoff für Rahmen oder Parts nie in reiner Form, sondern immer als Legierung auf. Daraus leiten sich auch die gebräuchlichen Bezeichnungen wie etwa 2014, 6061 oder 7005 ab, die auf dem amerikanischen Standard ASTM (American Society for Testing and Materials) beruhen. In der DIN-Norm lautet die Bezeichnung etwa für Al 7005 „AL Zn4,5Mg1,5Mn“.
Darin lassen sich die jeweiligen Legierungsanteile und deren prozentuale Anteile ableiten. Alu aus der 2000er-Serie besitzt etwa als Hauptlegierungsanteil Kupfer. Das führt zu einer wesentlichen Steigerung der Festigkeit, verringert aber auch die Schweißbarkeit erheblich, weshalb der Werkstoff nur bei schweißnahtfreien Parts wie Vorbauten oder Sattelstützen zum Einsatz kommt. Die meisten Parts und Rahmen bestehen jedoch aus den gut mit Schutzgas schweißbaren Legierungen der 6000er- und 7000er-Serie. Hier kommen vor allem Magnesium, Silizium und Zink als Hauptlegierungsanteile zum Einsatz.
Um die gewünschte Festigkeit zu erhalten, müssen Aluminium-Legierungen einen speziellen Wärmeprozess durchlaufen. Die Zusatzbezeichnung T6 neben der Werkstoffbezeichnung weist darauf hin und bedeutet: lösungsgeglüht und wärmeausgelagert. 7000er-Alu besitzt im Vergleich zum 6000er eine etwas höhere Festigkeit, gleichzeitig steigt aber auch die Sprödigkeit.
Im Vergleich zu Carbon reagiert Aluminium weniger empfindlich gegen Impacts, wie etwa bei einem Sturz. Eine kleine Delle ist in der Regel nur ein optisches Problem. In Sachen Dauerfestigkeit bleibt Alu aber gegen Carbon chancenlos. Ermüdungsrisse treten bei dem Leichtmetall deutlich häufiger auf. Auch beim Komfort kann ein Alu-Rahmen kaum punkten. Hardtails leiten Schläge am Hinterrad gerne ungefiltert an die Wirbelsäule weiter. Weniger ein Problem bei Fullys, denn hier federt der Dämpfer die Stöße ab.
Mehr Bike Know-how:
Gewinnen Sie einen Volvo XC60:
Stahl: Unanfällig vor Überlastung
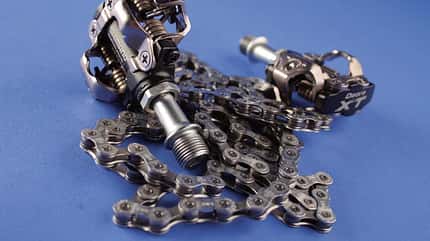
„Steel is real“ lautet der Leitspruch von Stahlliebhabern. Die Vorzüge des Materials liegen vor allem in der hohen Festigkeit und Sicherheit gegen Überlastbrüche. Drücken, Ziehen und Quetschen führt bei Stahl zu einer Kaltverfestigung und somit zu einem Anstieg der Festigkeit.
Stahlrohre von heute besitzen etwas größere Durchmesser, um die Steifigkeit zu erhöhen. Die Wandstärke beträgt an manchen Stellen nur noch 0,4 Millimeter. Bei noch dünnerer Wandstärke wäre die Beul-Gefahr allerdings zu hoch.
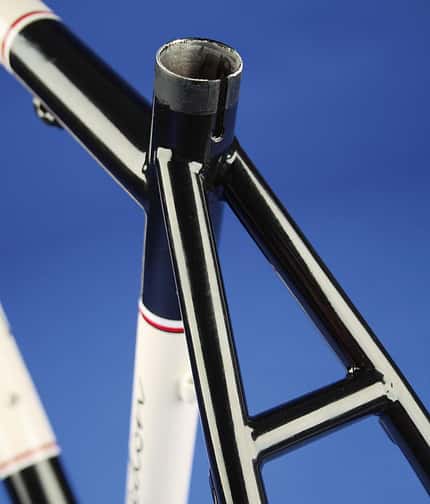
Bei der Verarbeitung gibt es viel Erfahrungswerte, dennoch bleibt die Rahmenfertigung ein aufwendiges Unterfangen.
Sowohl die Bearbeitung des harten Materials als auch das Schweißen erweist sich als deutlich schwieriger und aufwendiger als etwa bei Alu und rechtfertigt auch die höheren Preise in der Hochleistungsklasse. Neben dem Schweißen werden Stahlrohre auch immer noch mit oder ohne Muffen gelötet.
Als Ausgangsmaterial für den Rohrsatz dient in der Regel die Legierung 25CrMo4 (0,25 % Kohlenstoff, 1 % Chrom und Spuren von Molybdän). Diese Grundlegierung verfeinern die Hersteller schließlich mit weiteren Legierungselementen und kochen so die Stahlsorte mit den bestmöglichen Eigenschaften.
Gegen Korrosion helfen Oberflächenbehandlungen wie Phosphatieren und Pulverbeschichten. An der Rohrinnenseite erfolgt oft eine Hohlraumversiegelung.
Mehr Bike Know-how:
Gewinnen Sie einen Volvo XC60:
Titan: Werkstoff für die Ewigkeit
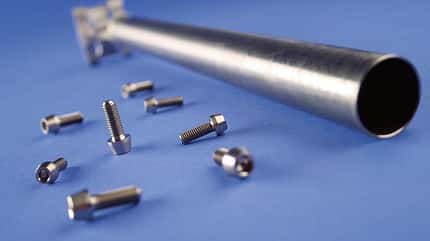
Dünne Rohre, zarte Schweißnähte und der gräulich schimmernde Look stehen unverwechselbar für den Edelwerkstoff Titan. Dabei handelt es sich gar nicht um ein Edelmetall. Das Material korrodiert nämlich an der Oberfläche und bildet dadurch erst diesen speziellen Farbton.
Die Oxidschicht bildet einen fast undurchdringlichen Schutz, der eine weitere Oberflächenbehandlung unnötig macht. Herstellerbezeichnungen sind deshalb in der Regel aufgeklebt oder eingraviert.
Titan erreicht Festigkeiten, die fast an Stahl heranreichen und bringt dabei etwa 40 Prozent weniger Gewicht auf die Waage. Beeindruckende Eckdaten, die sich vor allem Tuning-Fans zunutze machen. Titan-Teile ersetzen typische Stahl-Parts wie Achsen oder Schrauben und sparen so Gewicht.
Die nahtlosen Rohre bestehen in der Regel aus der Legierung TiAl3V2,5 (3 % Aluminium, 2,5 % Vanadium), sind bis zu zweifach konifiziert und weisen Wandstärken von mindestens 0,6 Millimeter auf. Flache Teile wie Ausfallenden fertigen die Rahmenbauer häufig aus dem hochfesten Plattenmaterial Ti6Al4V. Rohrhersteller Reynolds bietet mittlerweile aber auch nahtlose Rohrsätze aus dieser Legierung an.
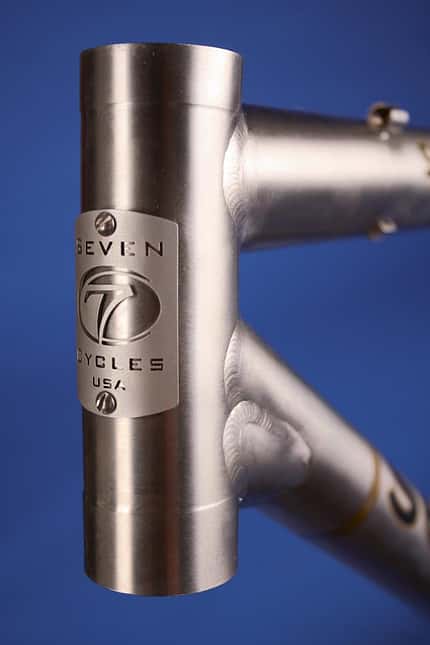
Auf dem Trail sorgen die dünnen Rohre, ähnlich wie Stahl, für guten Komfort und eignen sich deshalb besonders für die Fertigung von Hardtail-Rahmen. Die relativ hohe Flexibilität der Rohre geht allerdings etwas auf Kosten der Steifigkeit.
Der Knackpunkt bei Titan liegt in der Fertigung. Nur wenige Hersteller beherrschen den sicheren Umgang mit dem heiklen Material. Bei höheren Temperaturen zeigt sich Titan plötzlich extrem korrosionsempfindlich.
Schweißen gelingt nur mit Hilfe von Schutzgas, das die Naht ununterbrochen und lückenlos umgibt. Der Verzug durch den Schweißprozess darf nicht zu groß ausfallen, denn der Rahmen lässt sich anschließend kaum noch richten.
Aufwendige Fertigung und teurer Rohstoff treiben die Verkaufspreise enorm in die Höhe. Wer aber das Geld in einen Titanrahmen investiert, erhält gewiss einen Partner fürs Leben.
Mehr Bike Know-how:
Gewinnen Sie einen Volvo XC60:
Die Fertigungsmethoden im Rahmenbau
Schweißen
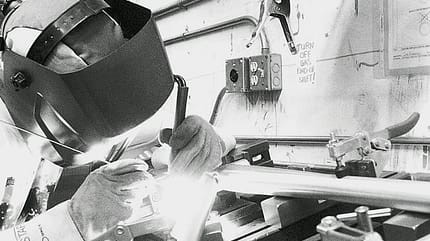
Die typische Fügetechnik für Metalle. Dabei schmelzen die Teile an den Verbindungsstellen auf und werden mit oder ohne Zusatzstoff miteinander verbunden (Bild rechts). Gegen Korrosion kommt Schutzgas zum Einsatz.
Löten
Traditionelles Verfahren zum Fügen von Stahlrohren. Funktioniert mit oder ohne Muffen. Anders als beim Schweißen schmilzt beim Löten nur der Zusatzstoff und verbindet die Teile.
Kleben
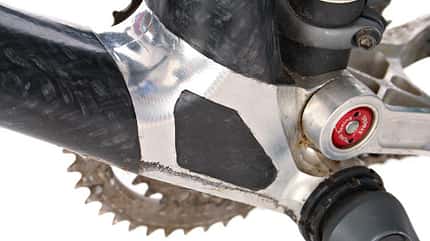
Hauptanwendungsgebiet Carbon. Gewinnt aber auch bei metallischen Werkstoffen an Bedeutung. Die Festigkeiten sind enorm, der negative Wärmeeinfluss beim Schweißen fällt weg, und es lassen sich unterschiedlichste Materialien miteinander verbinden (Bild links).
Konifizierung
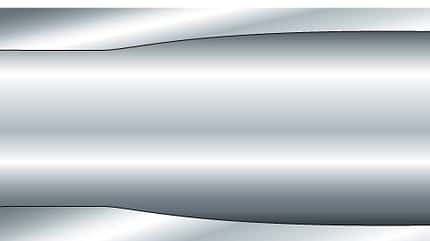
Variiert der Innendurchmesser und somit die Rohrwandstärke, spricht man von Innenkonifizierung (Bild rechts). Änderungen des Außendurchmessers bezeichnet man als Außenkonifizierung. In beiden Fällen lässt sich Gewicht und Steifigkeit der Rohre steuern. Je nach Anzahl der Wandstärkenänderung spricht man von einfach-, zweifach-konifiziert usw.
Hydroforming
Ein Wasser-Öl-Gemisch presst das Rohr unter hohem Druck gegen eine Werkzeugform und ermöglicht so völlig neue Querschnittsformen. Dadurch lässt sich die Steifigkeit optimieren – die individuelle Optik wird zum Wiedererkennungsmerkmal.
Mehr Bike Know-how:
Gewinnen Sie einen Volvo XC60:
Interview: Wohin geht’s in der Zukunft?
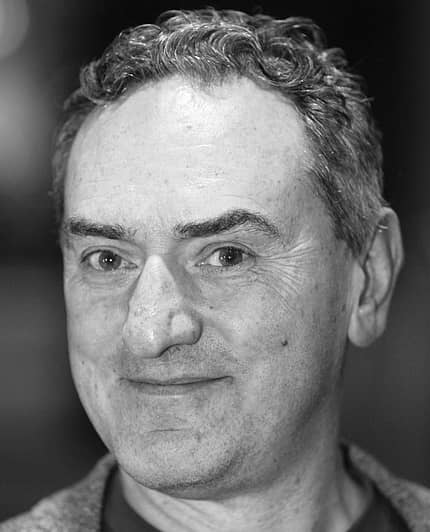
Rahmen bestehen mittlerweile aus unterschiedlichsten Werkstoffen. In welchem Material liegt die Zukunft?
Probst: In der Breite bleibt nach wie vor Aluminium Werkstoff Nummer eins. Die Fertigung von Carbon ist schwieriger und aufwendiger und auch die Kosten sind erheblich höher. Aber bei Hardtails, ab einer Grenze von etwa 2000 Euro, könnte Carbon in Zukunft durchaus die dominante Rolle übernehmen.
Und wo liegt die Zukunft für die Werkstoffe Stahl und Titan?
Probst: Beide bleiben als Rahmenwerkstoff nach wie vor nur ein Randthema. Titan ist für den Massenmarkt einfach zu teuer. Aber auch hochwertige Stahlrahmen erfordern einen höheren Fertigungs- und Kostenaufwand als Modelle aus Alu. Nur mit teuren Werkzeugen lässt sich der harte Werkstoff bearbeiten.
Gibt es noch andere Werkstoffe, die im Fahrradbau eine Rolle spielen könnten?
Probst: Im Bereich der Kunststoffe gibt es noch Potenzial. Es hat bereits Versuche mit Thermoplasten gegeben, das Projekt scheiterte allerdings. Nach heutigem Stand der Technik wäre vielleicht einiges mehr möglich.
Mehr Bike Know-how:
Gewinnen Sie einen Volvo XC60:
Fazit: Jedes Material hat Stärken und Schwächen
Alu gilt als der leicht zu verarbeitende, kostengünstige Universalwerkstoff, Stahl macht bei Verschleißfestigkeit und Überlastschutz die beste Figur, und das unempfindliche Titan gilt als Werkstoff für die Ewigkeit. Kohlefaser punktet gegenüber den Metallen vor allem durch nie erreichte Steifigkeits/Gewichts-Werte. Doch während die Hersteller bei der Verarbeitung metallischer Werkstoffe bereits jahrzehntelang Erfahrung sammeln konnten, birgt das Verkleben des relativ jungen Werkstoffs Carbon immer noch gewisse Risiken.
Mehr Bike Know-how:
Gewinnen Sie einen Volvo XC60: